Steel Wire Rope Use & Maintenance
In this section you will find essential details on the use and maintenance of steel wire rope.
Instructions for Use of Steel Wire Rope
Before first use
please check that:
a)the steel wire rope is according to order;
b) the steel wire rope and the packaging aren't damaged;
c) the steel wire rope diameter, is according to below;
d) that certificates exsists;
e) that the steel wire rope is suitable for the application;
f) that the equipment that the steel wire rope is going to be used together with is in working condition.
Use in hazardous conditions
If the steel wire rope is to be used in hazardous conditions a risk evaluation is to be done. The WLL of the steel wire rope should be decided or adjusted according to this. Example of such conditions are offshore, lifting people or dangerous load.
Use in Adverse Environments
Temperature effect on working load limit (WLL)
Account should be taken of the maximum temperature that can be reached by the wire rope sling in service. This is difficult in practice but underestimation of the temperature should be avoided.
The table below summarises the necessary de-rated working load limits of a sling due to temperature, taking into account the type of rope termination, the ferrule material and the core of the rope.
When wire rope slings are to be used in temperatures below -40 °C CERTEX should be consulted.
The use of wire rope slings within the permissible temperature ranges given in the table does not require any
permanent reduction in working load limit when the rope is returned to ambient temperature.
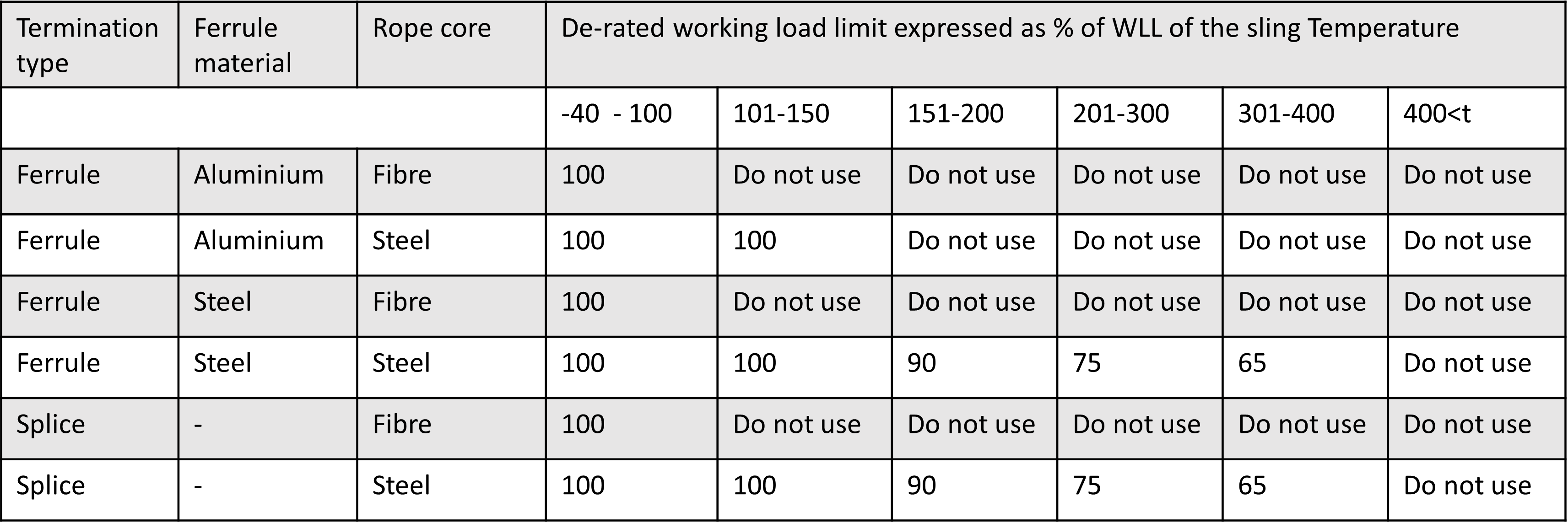
-------------------------------------------------------------------------------------------------------------------------------------------------------------------------------------------------------------------------------------------------------------------------------------------------
Instruction for Handling of Steel Wire Rope
Following instructions and warnings are issued to give guidelines for safe installation and handle. Warning texts point at areas where large risk for considerable reduction of life of the steel wire rope and/or damage on equipment and to person by wrong handle exists.
WARNING! Handle and installation of steel wire ropes shall always be performed by a person with knowledge and education about valid safety regulations.
Packing
Wire rope is generally delivered in a coil, plywood or wooden reel. On the European mainland a cross reel is also common. Please specify packaging when ordering.
Lifting & Handling
Ensure that the rope is not damaged by fork lifts or other handling equipment, by lifting or handling.
WARNING! Wrong handling/lifting can damage the rope.
Storage
Steel wire ropes shall be stored in a dry and well ventilated location. Cover with waterproof material by outside storage. Rotate the reel periodically during long periods of storage, partuculary in warm environments. The ropes shall be examined regulary and lubricated if necessary.
WARNING! Incorrect storing can cause damage on the wire rope. Never store the rope in environment with highly various temperature.
Unwinding
Wrong coiling can cause serious damage to the steel wire rope. Coil or wind according to the following:
- Reels should be rolled out or alternatively placed on a turnable centre.
- Cross reels and drums should be placed on a shaft that allows it to rotate.
- Wind and unwind the rope in the same direction.
- In some cases it may be necessary to brake the drum.
WARNING! Wrong "opening" of packing can cause serious injury to personnel, first ensure that the rope is under control.
Never pull a rope from a stationary reel or drum - due to the risk of kinking.
Cutting
Usually ropes are supplied in cut lengths, with "tapered" ends made by annealing. If the rope is required to be cut during assembly the rope shall be seized each side of the cut, to prevent damage from opening strands and/or changing lay length.
One seizing either side of the cut is normally sufficient for preformed ropes. For "rotation resistant" and special wire ropes a minimum of two seizings each side of the cut will be necessary. The length of each seizing should be a minimum 2 x rope diameter.
Cutting should be made with a high speed abrasive disc cutter, cutting torch or other suitable mechanical or hydraulic shearing equipment.
After the rope has been cut the seizing should be left until all the wires are welded or otherwise secured.
WARNING! Incorrect cutting can cause damage to the rope. Be extra careful when cutting rotation resistant ropes.
Use safety goggles and other appropriate safety equipment when using a disc cutter or other mechanical or electrical devices.
"Breaking In"
After the rope has been installed and before it is taken into operation, several run-throughs of normal operation circle should be carried out under light load to let the rope adjust itself to the actual operating conditions.
Drum - Groove
Check the general condition of the drum. If the drum is grooved, check the radius and pitch are compatible with the diameter of the new rope.
WARNING! The drum can in some cases cause damage to the rope and lead to early discard. If the drum diameter is too small this can cause permanent distortion to the rope which will cause to early discard of the rope.
Drum - Correct Coiling
The rotation direction and the attachment point of the rope determines whether right or left hand lay rope should be used. To determine the correct rope the following rule should be followed:
Right thread groove on the drum - left hand lay rope.
Left thread groove on the drum - right hand lay rope.
WARNING! Incorrect choice of lay can adversely affect rope performance.
Pass a shaft through the reel and place the reel in a suitable stand which allows it to rotate and be braked to avoid over run during installation. Where multi-layer coiling is involved it may be necessary for the reel to be placed in equipment which has the capability of providing a back tension to the rope as it is being transferred from reel to drum. This is to ensure that the underlaying (and subsequent) laps are wound tightly on the drum.
WARNING! Incorrect coiling may cause severe damage to the wire rope as well as its performance.
Drum - Multiple Layers
Multiple layers of wire on the drum can cause deformation (flattening, distortion etc) in the lower layers if the wrong rope construction is used and/or by incorrect winding.
Drum - Fleet Angle
Too large a fleet angle can cause excessive wear of the rope against the adjacent wrap on the drum. This can also lead to torsional problems.
Drum - Connection
When installing a new rope a cable sock or alternatively a welded pad eye can be used as connection between the old and new rope.
Individual turn between two ropes when installing can be possible with a swivel, which avoids turn being transmitted from the "old" rope into the new rope.
WARNING! Always check that "rope torque" does not exist during installation. A cable sock or other connection should be equipped with a swivel.
Drum - Capacity
The following formula gives an approximate indication of the length of a rope of a given diameter (d), which can be installed onto a drum.
Rope length (m) = (A+B) x A x C x π x 106 / d2
A, B and C are quoted in metres and d in millimetres.
Note that ropes are normally manufactured to a maximum oversize tolerance of up to 5%.
Lubrication of wire ropes
Running wire ropes must be lubricated regularly when in operation. Regular treatment with suitable lubricants may significantly increase rope service life.
Contact CERTEX for further advice and help on lubrication
Examination
At examination of steel wire ropes attention shall specially be drawn to the parts of the rope that are, known from experience, exposed to wear and damage.
Wear, broken wires, distortion and corrosion are more common visible signs of deterioration.
Wear is a normal feature of rope service and the correct rope construction ensure that it remains a secondary aspect of deterioration. Correct lubrication of the rope may help to reduce both outer and inner wear.
Broken wires are normally feature of rope service towards the end of the rope's life, resulting from bending fatigue and wear. The local break up of wires may indicate some mechanical fault in the equipment. Correct lubrication in service will increase fatigue performance.
Individual broken wires shall be attended to by removing the wire, see figure.
Distortions are usally as a result of mechanical damage, and if severe, can considerably affect rope strength.
Corrosion, both outer and inner, indicate unsuitable grease. Pitting on the external wire surface can result in breaking wires. Inner corrosion occurs in some environments when lubrication is inadequate or of unsuitable type. Reduction in rope diameter will frequently guide the observer to this condition, but confirmation can only be made by inner examination of the rope
WARNING! Do not cut the wire, bend it until it breaks and let the break be close to the inner of the rope construction. This reduce the risk for ends of wires sticking out of the rope
-------------------------------------------------------------------------------------------------------------------------------------------------------------------------------------------------------------------------------------------------------------------------------------------------
Instruction for Discarding Steel Wire Rope
Rope Discard
Discard the wire rope in accordance with current regulations or according to the manufacturers recommendations.
Only a qualified and experienced person should be responsible for discard.
The pictures show typical examples of wire rope deterioration.
WARNING! Failure to take adequate precautions could result in injury.
Please see chart below:
Ropes having outer strands of Seal construction where the number of wires in each strand is 19 or less (e.g. 6 x 19 Seal) are placed in this table two rows above that row in which the construction would normally be placed based on the number of load bearing wires in the outer layer of strands.
a) Filler wires are not regarded as load-bearing wire and are not included in the values of n.
b) A broken wire has two ends (counted as one wire)
c) The values apply to deterioration that occurs at the cross-over zones and interference between wraps due to fleet angle effect.
d) Twice the number of broken wires listed may be applied to ropes on mechanisms whose classification is known to be M5 to M8.
e) d= nominal diameter of rope
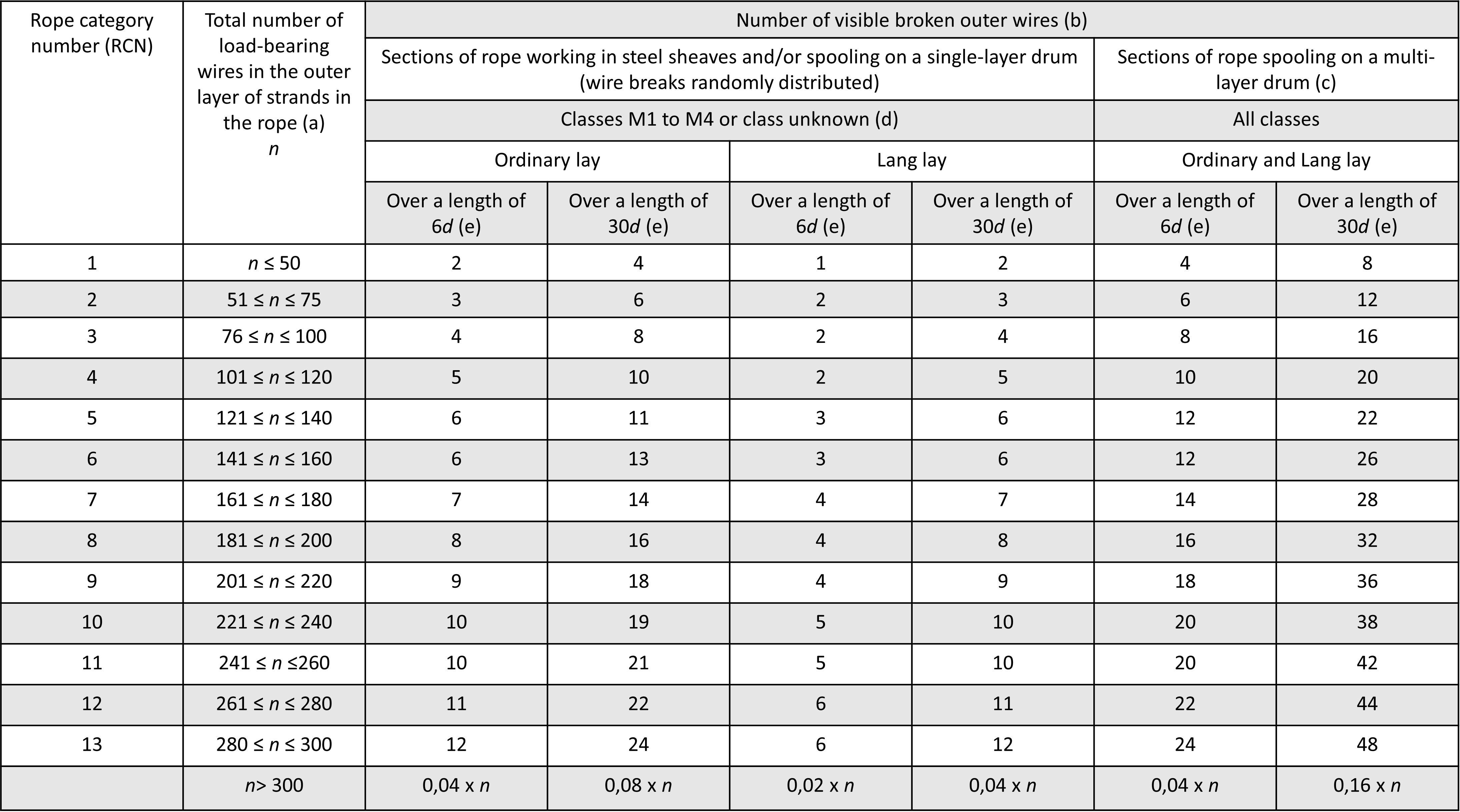
Technical Guidance
READ MORETraining Courses
ENQUIRE NOW