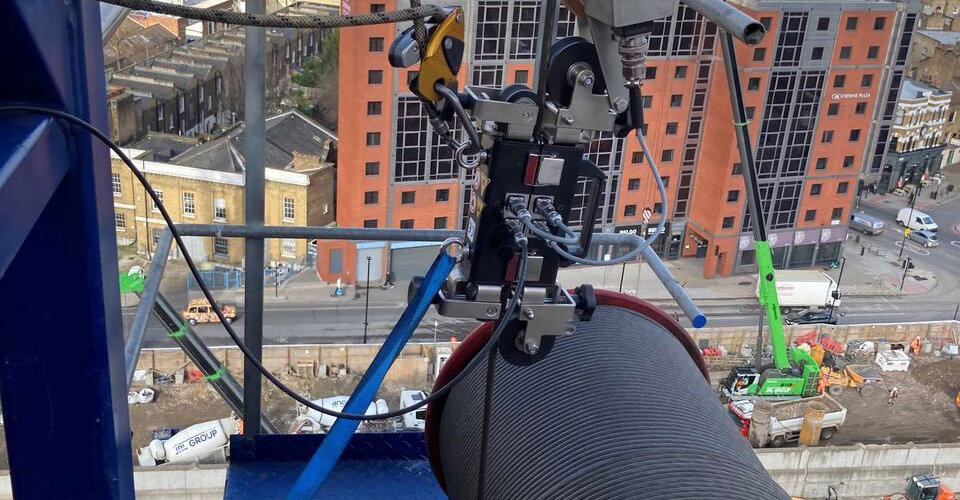
Certex UK Expands MRT Services
Certex UK has expanded its magnetic rope testing (MRT) capability, amid wider recognition of its benefits versus visual inspection.
MRT is a method of inspecting steel wire rope. It is more efficient and safer than traditional, visual inspection largely because of the complexity of wire rope and the fact that simply looking at a rope only allows you to inspect what you can see with the naked eye. What’s going on inside remains a mystery.
MRT isn’t a new concept—it has been around in some industries longer than others—but its benefits remain underrated in many sectors. The MRT method is a non-destructive, magnetic, and contactless procedure that allows Certex to detect broken wires, distortions, and corrosion within steel wire ropes. It was first seen in the cableways sector to inspect the haulage and carriage—and to identify internal and external defects.
Certex powers its MRT services with products manufactured by Italian firm AMC Instruments, which was acquired by Certex’s owners Axel Johnson International AB in 2018, becoming part of the Lifting Solutions Group. Since then, the Certex-AMC partnership has pioneered its use, even in markets that were initially slower to introduce it to inspection routines.
Certex has been providing MRT expertise for years but, today, it provides MRT services to more sectors than ever before, with stakeholders at crane companies, docks, shippers, offshore oil and gas, steel works, power stations, wind farms, elevators, and building facilities, all recognising that MRT is the only tool that can provide a quick and accurate assessment of the whole rope condition, not only what is immediately apparent during a routine, pre-use inspection. As a result, Certex has recently expanded its dedicated teams based in Great Yarmouth and Scotland, albeit with a primary focus on offshore and onshore energy industries.
Ian Shaw, divisional manager, engineering services, at Certex UK, said: “The benefits of MRT have increased the quality of inspections by giving the inspector the ability to review the internal condition of the wire rope—protrusion, external fatigue broken wires, valley breaks, internal defects, internal corrosion—and by giving more confidence to the end customer via this more thorough examination of the rope. Remember, a rope is originally fitted in many applications by an OEM [original equipment manufacturer] but as it is a consumable item, it wears and expires before the equipment it is fitted to. MRT is thusly an imperative safety measure in modern industry.”
Notably, the most recent version of ISO 4309 has included MRT as an assessment method for the inspection of generic heavy-lifting steel wire ropes. The standard also references localised faults (LF), sometimes called localised defects (LD); and loss of metallic area (LMA). As Shaw explained, the LF signal is the main most reliable technique in this field, and it is completely regulated by international standards; it is the oldest among MRT systems. This well-known signal measures the leakage of magnetic flux, in presence of a defect on a magnetised object, such as a wire rope. Broken wires and corrosion can be detected by the LF technology, for example.